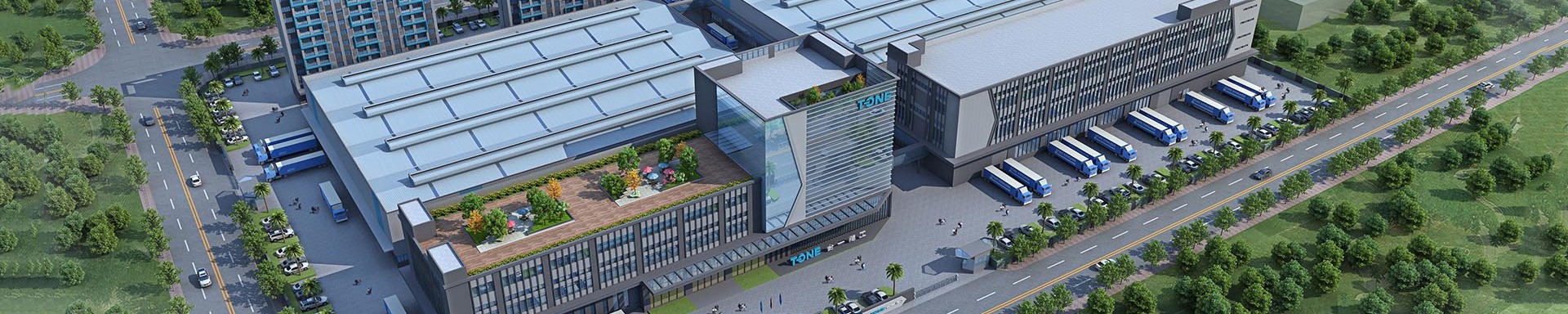
Vacuum Transfer Corrugated Paperboard Die-cutter Machine
1. T-ONE die-cutter machine with orginal SUN automation feeding system ,feeding accuracy and stable are promised
2. Fully vacuum transferring system applied to the die-cutter machine ,the surface of the feed roller is ceramic roll, which increases wear resistance and prolongs life
- T-ONE
- Foshan,China
- Information
- Video
- Download
T-GC1200X2800 Vacuum Transfer Corrugated Paperboard Die-cutter Machine
Main Parameters:
Model | T-GC618 | T-GC920 | T-GC924 | T-GC1224 | T-GC1228 | T-GC1428 | T-GC1628 | T-GC1632 | T-GC1636 |
Max. Speed(pcs/min) | 350 | 300 | 300 | 250 | 230 | 220 | 180 | 180 | 160 |
Max Feeding Size(mm) | 600×1800 | 900×2000 | 900×2400 | 1200×2400 | 1200×2800 | 1400×2800 | 1600×2800 | 1600×3200 | 1600×3600 |
Min Feeding Size(mm) | 200×435 | 270×600 | 270×600 | 320×600 | 320×600 | 365×600 | 450×600 | 450×600 | 450×600 |
Skip Feeding (mm) | 800×1800 | 1200×2000 | 1200×2400 | 1500×2400 | 1500×2800 | 1700×2800 | 1900×2800 | 1900×3200 | 1900×3600 |
Max. Printing Area(mm) | 600×1760 | 900×1960 | 900×2360 | 1200×2360 | 1200×2760 | 1400×2760 | 1600×2760 | 1600×3160 | 1600×3560 |
Min. Slotting Reverse knife(mm) | 180×55×180×55 | 240×65×240×65 | 240×65×240×65 | 260×65×260×65 | 260×65×260×65 | 260×65×260×65 | 260×65×260×65 | 260×65×260×65 | 260×65×260×65 |
Min. Slotting Normal knife(mm) | 110×110×110×110 | 130×130×130×130 | 130×130×130×130 | 130×130×130×130 | 130×130×130×130 | 130×130×130×130 | 130×130×130×130 | 130×130×130×130 | 130×130×130×130 |
Slotting Depth (mm) | 200 | 250 | 250 | 300 | 300 | 350 | 400 | 400 | 400 |
Product Detailed:
Feeder Unit
Ø Continuous or skip feeding is available with counter.
Ø Lead Edge Feeder with motorized feeding stroke adjust and reduce the pull roll pressure.
Ø Original imported SUN Lead Edge Feeder to promise long - term feeding precision and stability.
Ø Several row brushes and anti-static system to keep the paperboard clean before coming into printer unit, printing quality promised.
Ø Main motor is protected from start-up when units are not fully closed and locked.
Printer Unit with Vacuum Transfer
Printing Cylinder
Ø High grade steel ground and chrome-plated.
Ø Run stable with dynamic balance done.
Ø Available with Matthews system, on the two ends with locking system to promise printing plate precisely putting .
Ø Full groove for hanging strip insert, specification is 10mmx3mm.
Ø Foot pedal for printing cylinder turning to hang and take off the printing plate.
Pressing Roll
Ø Vacuum for paperboard transfer(ceramic coated wheel with prolonged life).
Ø High grade steel ground and chrome-plated.
Ø Run stable with dynamic balance done.
Ø Pressing roll gap PLC control, range from 0-12mm
Ceramic Anilox Roll
Ø High grade steel ceramic -plated, ground and laser engraving.
Ø Evenly distributed dot for evenly ink distribution.
Ø Printing plate and rubber roll are extended.
Ø Anilox roll gap PLC control, range from 0-12mm.
Rubber Roll
Ø Wear resistant rubber wrapped around the steel pipe surface.
Ø Fixed speed difference between rubber roll and anilox roll, so the ink scrapping will be much better.
Ø Specially ground for the rubber roll center, ink transfer will be much better
Ø Rubber roll gap PLC control, range from 0-12mm
Registration Adjust System
Ø Printing registration controlled by servo motor
Ø Magnetic clutch brake system: when units are open for registration adjust and washing, the brake system stop the gear running. And the gear stay in the same position.
Ø Lateral register controlled by PLC (±10mm).
Ø After printing plate cleaning, auto coming back to the original place.
Ink Circulation System
Ø Pneumatic single diaphragm pump,stable inking and easy maintaining.
Ø Indicator will be on if abnormal inking.
Ø Filter applied to remove the impurity to protect anilox roll.
Ø Stainless ink basin.
Ø Automatic washing system; after ink return finished and washing will be auto on
Ø SUN Single Doctor Blade System optional
Factory Show
There are several solutions: 1. Check the air pressure, the air pipe of the arm lock cylinder should not leak air, and all the air pipes should not leak air. 2. Adjust the pressure and position of the impression roller. 3. Adjust the parallelism of the impression roller and the printing cylinder. 4. Tighten the ratchets at both ends of the printing plate to make the printing plate tensioned....more